The blog for rail freight professionals
Knowledge, news, trends and tips: Find everything you need to know about the rail freight industry in this section.
%20(1).png)
The myth of the universal TMS: Why one tool can’t govern every mode of transport?
Discover why a universal TMS doesn’t work for all transport modes, and how Everysens’ specialized rail solution solves industry-specific challenges with its tools.
May 21, 2025
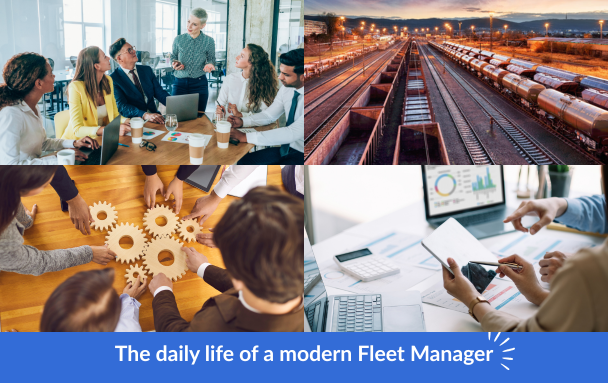
Be the brain behind the wheels. Become a Fleet Manager!
What does it really mean to be a Fleet Manager today? Between KPIs, real-time data, and environmental impact, discover how Everysens turns a complex mission into a powerful strategic role.
May 6, 2025
.jpg)
Track wagons like never before, no GPS needed!
Stop guessing where your wagons are. With the new Manual Wagon Tracking Without GPS feature in TVMS, fleet managers gain real-time, accurate visibility without expensive hardware or complex updates.
April 24, 2025
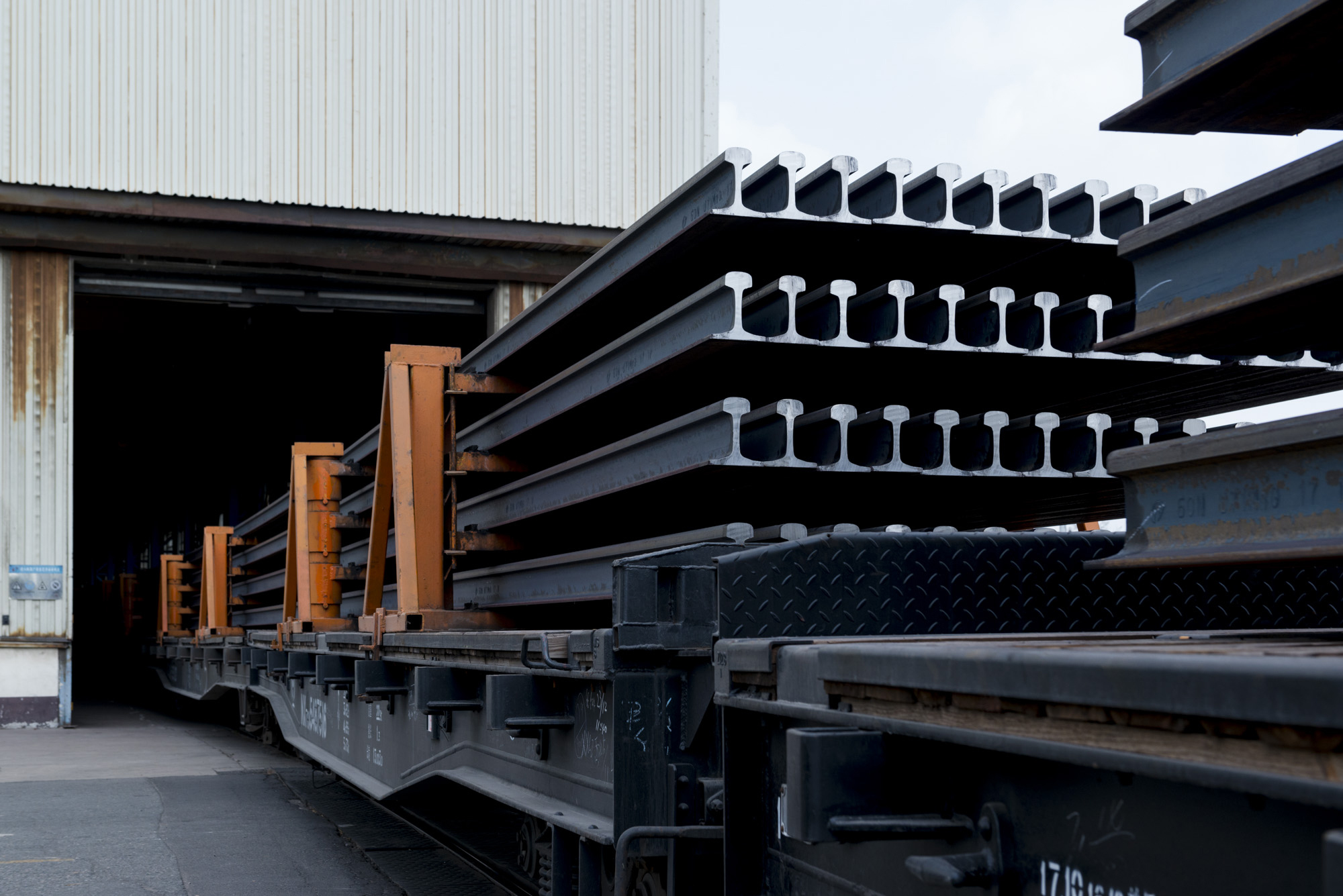
Beyond limits: How People & Technology are changing steel logistics.
Steel logistics is shifting from reactive problem-solving to strategic optimization. Discover how digital tools and lessons from other industries are transforming rail freight.
April 23, 2025
No article found. Change your search criteria.
Take it from our clients
Meet the driving forces that transform the rail freight industry